Abstract: The reasons for the quality problems in the iron-based alloy surfacing on the sealing surface of the nuclear manual valve body are analyzed, and the quality control measures of the surfacing layer of the valve proposed after changing the surfacing process parameters and evaluating the process's stability are introduced.
1.
Overview
API 000 is the third-generation pressurized water reactor nuclear power technology. In order to reduce the radiation level of the unit after the operation, the cobalt containing materials are strictly restricted. Therefore, iron-based alloys are selected for the hardfacing of the sealing surface of the API 000 manual
valve with small diameters.

Figure 1 Valve bodies and surfacing positions
Table 1 Parameters of the surfacing process
Filler metals |
Welding methods |
Current A |
Voltage V |
Welding speeds mm/min |
Heat input kJ/mm |
ERFeCr-A5 |
GTAW |
150 to 175 |
11 to 17 |
120 to 200 |
1.49 |
2.
Analyses
2.1
Surfacing
The material of the valve body (Figure 1) is stainless steel F304, and the nominal size is less than and equal to 50 mm. The size of the surface to be welded is small, which is a typical deep hole surfacing. In the welding process, the surface of the base metal has a poor holding effect on the shielding gas, which easily causes the welding layer to be insufficiently protected. According to the structural characteristics of the valve body, manual tungsten argon arc welding is used for surfacing. The American standard material SFA-5.21ErFeCr-A5 iron-based welding wire is selected based on the requirement for the welding material containing low cobalt. Before welding, the machined surface to be surfaced is subjected to liquid penetration testing. After confirming that there are no defects, two layers of iron-based alloys (Table 1) are surfaced by manual argon welding on the sealing surface. After welding, the surfacing layer should be processed smoothly, and the thickness of the sealing surface is from 2 to 3 mm.
2.2
Testing
After surfacing, the machined sealing surface was inspected with liquid penetration, and defects such as cracks were found on the sealing surface (Figure 2). In order to find out the reason and verify the reasonableness of the welding process, the surfacing parts of the valve body were disassembled and sampled for inspection (Figure 3).
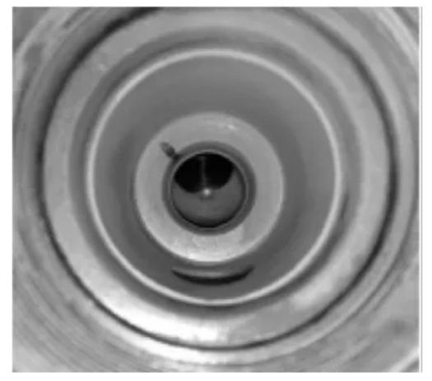
Figure 2 The defects of the sealing surface
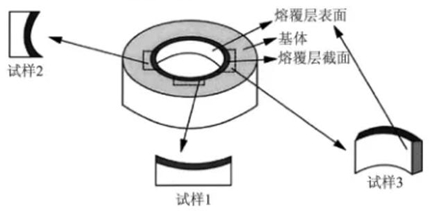
Figure 3 Sampling of the sealing surface
The chemical composition of deposited metal was analyzed by fluorescence spectroscopy, and the result met the requirements. The sealing surface was cut, sampled, polished, and corroded with aqua regia to make a metallographic sample. The metallographic micrograph (Figure 4) showed that the deposited metal and heat-affected zone were well fused; the structure was uniform and compact, without cracks, but there were black holes in the surfacing layer, which were mostly circular welding holes. A stress analysis on the sealing surface of the valve body was conducted, and the measuring point along the matrix to the fusion zone (Figure 5, Table 2) was selected. From the numerical analysis, it could be seen that the stress gradually increased from the base material along the direction of the surfacing layer, and the maximum stress was 147.6MPa. The welding heat input, the cooling rate of the welding seam and restraint degree of the base material to be welded were the main reasons for the great residual stress.
Table 2 The test results of stress MPa
Test points |
1 |
2 |
3 |
4 |
5 |
6 |
Stress |
147.6 |
106.9 |
125.8 |
101.4 |
132.5 |
83.4 |
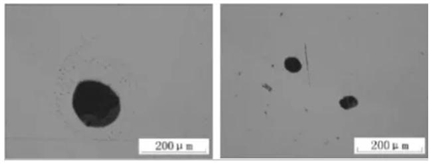
Figure 4 The microscopic morphology of sample 2 after metallographic corrosion
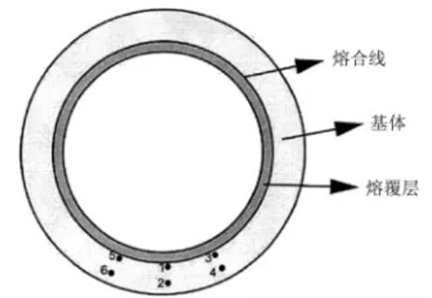
Figure 5 The test points of stress
2.3
Improvement
Through the analysis, the hard alloy cracks of the surfacing layer on the sealing surface of the valve body are caused by the internal holes and excessive residual stress in the surfacing layer. Because the residual stress in the surfacing layer is relatively great, stress concentration will be formed around the hole in the valve's surfacing layer when stored for a long time or under external force, which will cause the cemented carbide to crack along the hole, gradually expand, and finally form cracks. In order to avoid the formation of holes in the surfacing layer and reduce the residual stress caused by the surfacing process, the preheating of the valve body before welding, heat preservation and heat treatment of the post welding are provided. Reasonable preheating measures make the valve body thermally expand and reduce the tensile stress of deep hole surfacing on the sealing surface. Preheating and post welding heat treatments accelerate the diffusion of hydrogen and the removal of stress, and ensure that the cooling rate of the weld forms a small temperature gradient. At the same time, the tooling equipment has been improved so that good gas protection can be formed, and excessive air holes can be avoided during surfacing.
After an anatomical inspection of the resurfacing of the sealing surface of the valve body, the hole's diameter is reduced by geometric orders of magnitude, and the peak of the residual stress is improved. The success rate of the product's sealing surface is over 92%, which proves that the improved iron-based alloy hardened surfacing process is stable, reliable, reasonable and effective.