1. Overview
In polysilicon, coal chemical industry, power plant ash removal, mud and boiler slag discharge and other pipelines transporting materials, the valve's sealing part is subject to the sliding friction and wear of the sealing pair parts, withstands the high-speed impact of high-temperature and high-hardness gas-solid dual-phase mixture, flash evaporation and cavitation caused by high-pressure fluid, which in turn causes damage and exacerbates valve failure. Therefore, under severe working conditions such as powder conveying, wear resistance has become an important performance evaluation index for the valve.
2. Analysis
According to the conditions and mechanism of friction, there are many different forms of wear, such as abrasive wear, adhesive wear, fatigue wear and corrosion wear, and erosion wear. The commonly used parameters to characterize the wear properties of materials are wear amount, wear rates, wear degrees, wear resistance and relative wear resistance. The basic requirement for wear of wear-resistant materials is that the surface of the object must have good hardness. The surface hardness should exceed that of the abrasive, and at the same time, it should have good oxidation resistance at the working temperature. The most effective way to control or minimize wear is to improve the hardness and wear resistance of materials. Sintered tungsten carbide has good strength and surface finish. When it is used with other materials, the friction coefficient is smaller than that of steel, which can significantly reduce the friction force of the contact surface and effectively reduce the operating torque.
3. Features
The integrated sintered tungsten carbide is made by heating a mixture of tungsten and carbon at high temperatures. Most tungsten carbides have good hardness, and their microhardness is only next to diamond. The melting point is 2870℃, boiling point 6000℃, and relative density 15.63(18℃). The tungsten carbide is not easy to decompose under high temperatures and has good anti-oxidation ability. The investigation of on-site use shows that the wear resistance of tungsten carbide in the case of abrasive wear, erosion wear and scratch is 100 times higher than that of tool steel, stainless steel, iron and brass; its rigidity is 2 to 3 times higher than that of steel, and 4 to 6 times higher than that of cast iron and brass; the impact resistance is similar to that of hardened tool steel.
4. Applications
In coal gasification and polysilicon, high temperature, high pressure, strong corrosiveness, slurry and powder containing solid particles, the sealing pair formed by sprayed tungsten carbide hard alloys is adopted for valve discs and valve seats of conventionally used hard-sealed ball valves, venturi black water control valves, pulverized coal control valves, disc valves and slide valves. The thickness of the tungsten carbide coating is less than 2mm. The hardness is less than 60HRC, and the bonding force between the coating and the substrate is less than 1000psi. Spraying is usually carried out at a high temperature of 10,000°C, and the operating condition is harsh. The service life of the valve with 10,000 cycles is difficult to guarantee, which cannot meet the long-term stable production requirements of systems such as coal chemical slurry and polysilicon powder. Also, the strength of sprayed tungsten carbide is mainly provided by the base material. When the linear expansion coefficients of the two materials are great, the use is limited by the temperature, and it is difficult to exceed 450°C. The sealing pair formed by sprayed tungsten carbide hard alloys is adopted for valve discs and valve seats of new hard-sealed ball valves (Fig.1), Venturi black water control valves (Fig.2), pulverized coal control valves (Fig.3), disc valves (Fig.4) and slide valves, and the valve performance has been significantly improved.
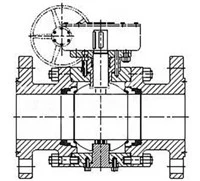
Figure 1 The new hard sealed ball valve
Figure 2 Venturi black water control valves
The integrated sintered tungsten carbide has the following advantages:
(1) Good hardness: the hardness of the integrated sintered tungsten carbide is greater than 80HRC, which can withstand high-speed scouring of multiphase granular media such as coal water slurry, coal powder, silicon powder, etc.
(2) High-temperature resistance: it can work at a high temperature of 750℃ for a long time, and its strength, bonding force and thermal expansion are not limited by temperature, which fully meets the high-temperature working conditions such as coal chemical industry.
(3) High-pressure resistance: the transverse fracture strength of the integrated sintered tungsten carbide reaches 4000MPa, which is more than 10 times the strength of conventional steel, and can work for a long time under the working pressure of 25MPa.
(4) Corrosion resistance: the integrated sintered tungsten carbide has stable chemical properties. Even it is heated, it is neither soluble in water, nor reacts with hydrochloric acid and sulfuric acid; it is not soluble even in aqua regia, which can meet the special requirements for corrosion for special industries.
(5) Wear resistance: the good hardness and stability of the integrated sintered tungsten carbide ensure the excellent wear resistance of the sealing auxiliary material, and meet the requirements of wear for special media such as coal powder and organic silicon. The hardness of silicon powder particles is 62HRC.
Figure 3 Pulverized coal control valves
Figure 4 Disc valves
(6) Scouring resistance: a sprayed tungsten carbide coating is adopted as the sealing surface for conventional valves, and the valve internals are subject to severe scouring. Usually, under the working temperature of 250°C, a honeycomb will appear within one month and the function will completely lose. The Venturi black water control valve and the pulverized coal control valve using integral sintered tungsten carbide as the control parts have a service life of 12 months at 450°C when other working conditions are the same. Frequently opened disc valves and slide valves can be opened and closed more than 300,000 times, which fully meets the requirements of operating for 8000h in industries such as the coal chemical industry over a long time.
(7)Good high-temperature motion performance: Both the ball and the valve seat adopt integral sintered tungsten carbide hard alloys, and their linear expansion coefficients are 1/3 to 1/2 of those of conventional steels, which effectively avoids high-temperature jamming of conventional valves and ensures their excellent motion performance under high-temperature differential conditions.
(8) Low friction: the use of sintered tungsten carbide wear-reducing gaskets prolongs the high-temperature service life of the gaskets. It is usually only 1/3 to 1/2 of the conventional matching materials because of its low friction coefficient, which greatly reduces the friction between the two, and the valve operating torque is reduced.
5. Conclusion
The integrated sintered tungsten carbide has good strength, good hardness, high melting point, good stability, low friction coefficient, wear resistance, scouring resistance and cavitation resistance, corrosion resistance, which is used for wear-resistant valve seals in harsh working conditions. It improves the applicability of the valve, expands the scope of use of the valve, prolongs the service life of the valve, ensures the performance indicators of the valve, and meets the development needs of the chemical industry.