The applicability of the current common test methods for ball valves is analyzed, and material tests, coating tests, tests of whole devices and simulation tests of working conditions are put forward; the test methods and processes are analyzed and discussed.
The working conditions of modern chemical equipment have the characteristics of high temperatures, high pressure, easy wear, high corrosion and high frequency. The switching frequency of the high-density polyolefin equipment is once per 30 seconds, and the switching time does not exceed 3 seconds. The pressure of the coal lock is 6.2MPa, temperature 150°C and switching frequency once per 30 minutes. The pressure difference of silicon chemical industry cyclone's blanking and returning conditions is 0.7MPa and temperature 280°C. The conveying media are silicon powder and methylchlorosilane, and the switching frequency is 4 times per hour. The pressure for the feed line and oil and gas line in the delayed coking unit is 0.4MPa, and the temperature is 500℃. The medium is residual oil or oil gas, and the medium is easy to coke; the pressure of the continuous reforming unit reforming catalyst station is 4.26MPa and temperature 427℃. The medium is adsorbent, and the switching frequency is 3 times per hour. Low-temperature methanol washing, ethylene and other reaction units also have the characteristics of low temperatures. For wear-resistant ball valves under severe working conditions, traditional test methods such as shell tests and tightness tests are only the minimum requirements for valve testing and cannot be fully applicable to harsh working conditions. Therefore, materials, coatings, whole devices, working condition simulation and other tests to ensure the safety and reliability of the valve quality should be conducted.
1. The dynamic analysis
1.1 Material strength
Valve materials for chemical plants are mainly carbon steel, austenitic stainless steel, martensitic stainless steel, duplex steel and nickel-based alloys. The elastic modulus of a material is to measure the ability of a material to resist elastic deformation and is an important parameter in valve design. For valves operating under severe operating conditions, in addition to referring to relevant standards, the selected material should be subjected to a test bar tensile test to obtain the actual elastic modulus of the material as a design basis.
1.2 Coating tests
The main content of the coating test is to test the adhesion, metallography, and hardness of the coating. The stress form of the coating is mainly extrusion. The sample was made and placed in a stretching and compressing testing machine to imitate the actual use of the ball and valve seat of the mating concave surface to carry out the extrusion test. The rigidity of the sphere used for the test should be ensured to prevent the coating from peeling off due to excessive elastic deformation, which may lead to misjudgment. In addition to metallographic tests, high-pressure water testing can also be used to detect the porosity of the coating. When the high-pressure water test was adopted, the pressure was maintained for different periods, and it was found that there was a leakage on the surface of the sphere (Figure 1).
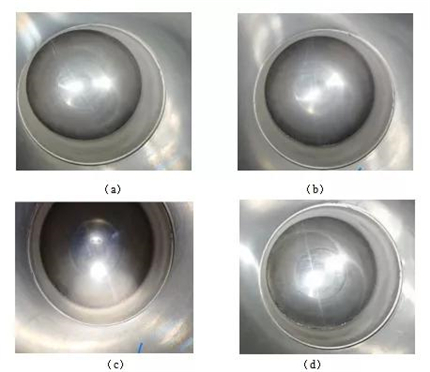
(A) Pressure maintaining for 1 minute (b) Pressure maintaining for 5 minutes (c) Pressure maintaining for 7 minutes (d) Pressure maintaining for 10 minutes
Figure 1 Leakages of coatings
Analyzing the coating test results, the leakage does not come from the sealing pair of the sphere and valve seat, but there is a leakage on the entire spherical crown surface. The tested sphere was cut, ground and polished, and the metallographic test of the coating was carried out on the metallographic testing machine. It was found that there were many and coherent pores in the coating (Figure 2), and the liquid medium leaks from the coating along the coherent pores. The much porosity of the coating is the main cause of leakages.
Figure 2 Metallographic test results of coatings
High-temperature adhesion tests should be conducted for the coating test. The applicable temperature of the coating material provided by the powder manufacturer is only the physical properties of the coating itself, and cannot represent the use temperature of the spherical coating. The bonding strength and temperature resistance of the coating with different materials at high temperatures must be determined through experiments. Put the sprayed sphere into a high-temperature heating furnace and it was slowly heated up as the heating furnace reaches the test temperature. Perform furnace cooling, air cooling, and water cooling to test the bonding strength of the coating at high temperatures (Figure 3). Use different cooling methods and the results obtained are also different; it is found in the experiment that the binding force is inversely proportional to the cooling rate.
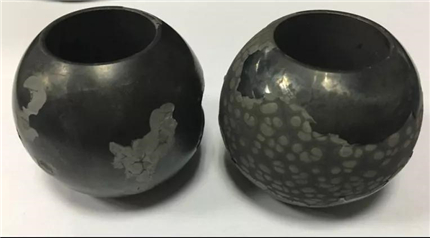
Figure 3 The cracking of the coating at the high-temperature test
The high-temperature thermal shock resistance of the coating is an indicator of the quality of the coating. Conventional mechanical bonding cannot meet the high-temperature and high-pressure thermal shock conditions, and the metallurgical bonding composite nano-spraying process can obtain excellent results (Figure 4).
Figure 4 Spheres and valve seats processed by the fusion plus nano-spraying composite process
2. The test and working condition simulation of the whole valve
2.1 The test of the whole valve
A test result for a single part cannot represent the overall performance, so the test for the whole valve should be carried out (Figure 5). The test for the whole machine can test the service life of the ball valve, strength of the drive chain, fatigue of the valve stem, high frequency and the wear resistance of the coating. Carry out no-load opening and closing tests, load opening and closing tests, no load degreasing tests, load degreasing tests and high-temperature load degreasing tests for the assembled valves. Among them, the high-temperature load degreasing test is the most stringent, which has very high requirements on the structure, process and materials of the valve. A valve with a reasonable structure and a reasonable process can pass multiple tests; otherwise, it will fail after several tests. The common damage of the valve includes cracking, straining, and adhesion of the coating, excessive fatigue of the valve stem after high-frequency work, the mating surface of the ball groove and valve stem being crushed by the valve stem, and the valve not being opened or closed well. The tested ball valve is disassembled, and the damaged parts are analyzed and researched. The structure, process and material selection are improved and optimized, and the experience is summarized through repeated tests to improve the overall performance of the valve.
Figure 5 Tests for the whole machine
2.2 The simulation of working conditions
The ball valve should be resistant to scouring, dust, and jamming. Therefore, it is necessary to restore the user's on-site working conditions as much as possible to perform the test (Figure 6). Before the valve leaves the factory, it should be fully tested to grasp its performance. The problem of the valve can be discovered in time through testing; improvements and optimizations should be carried out before leaving the factory, providing users with valves with reliable quality. Through the simulation test of working conditions, the valve materials and models can be selected according to different working conditions.
Figure 6 Simulation tests of working conditions
An analysis of the valve after the test (Figure 7) shows that the structure and accuracy are critical to the service life of the valve. The experiment is designed to reserve different expansion spaces for different temperatures, and a suitable structure is adopted according to the characteristics of the medium to ensure the fluidity of the medium. Through the life comparison test of valves with different sizes, it is found that the service life of the all-metal structure floating ball valve has nothing to do with the size. Valves of big sizes are more adaptable to different particle media while ensuring the same service life. The disadvantage is that the torque is too great, resulting in high prices for pneumatic valves. The trunnion ball valve with complex structure has poor adaptability to particulate media, and has the advantages of low torque and low prices.
Figure 7 The analysis of test results
Conclusion
Metal-seated ball valves used in harsh working conditions are essential to the normal operation of the entire chemical plant. It is not sufficient and imperfect to just carry out theoretical calculation and finite element analysis to shape the valve structure. Products related to the selection and design of valves are found, optimized and improved through the various tests on the coating and the whole valve. At the same time, a simulation test of the working condition is carried out based on the severe working conditions of the ball valve. The performance of the valve is tested under the conditions of simulating the actual working condition to ensure that the ball valve can operate normally under the bad working condition of the chemical plant.